What does the air compressor governor do?
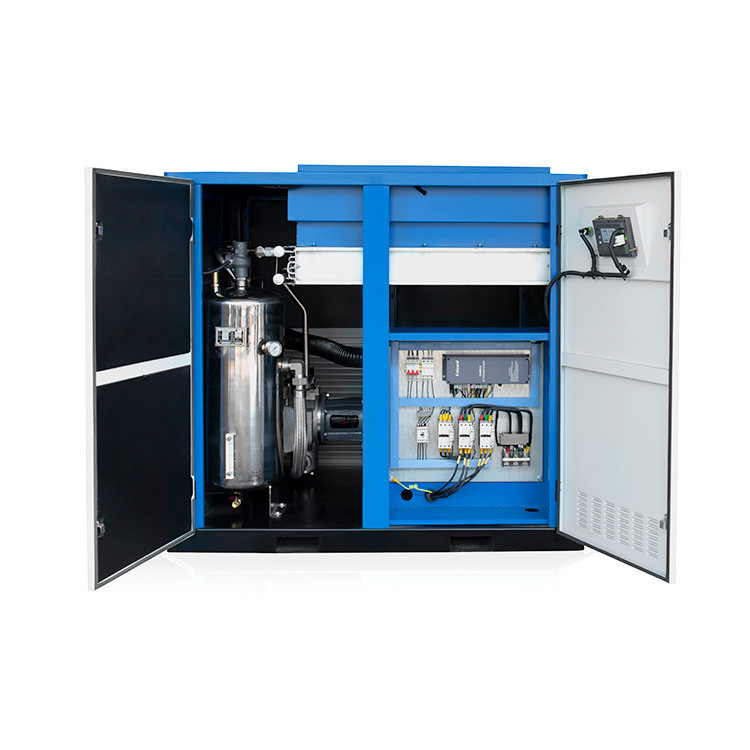
Demystifying the Role of an Air Compressor Governor: What
Does It Actually Do?
Introduction to air compressor governors
As an industrial professional, you may have
come across the term "air compressor governor" in your line of work.
However, do you truly understand what this crucial component does and how it
affects the performance of your air compressor? In this article, I will
demystify the role of an air compressor governor, explaining its function, how
it works, and why it is important in maintaining pressure for various
applications.
Understanding the function of an air compressor governor
An air compressor governor is a device that
regulates the pressure produced by an air compressor. Its primary function is
to maintain a consistent pressure level within the compressor, ensuring optimal
performance and efficiency. Without a governor, the pressure could fluctuate,
leading to potential damage to the compressor and other connected equipment.
The governor achieves this by monitoring
the pressure within the compressor's air tank and making adjustments to the
compressor's motor speed. When the pressure reaches a certain predetermined
level, the governor will signal the motor to slow down or stop, preventing the
pressure from exceeding the desired threshold. Conversely, when the pressure
drops below the set level, the governor will prompt the motor to increase its
speed, allowing the compressor to build up pressure until it reaches the
desired level once again.
How does an air compressor governor work?
To understand how an air compressor
governor works, it is essential to delve into its internal mechanisms. The
governor consists of several key components, including a pressure sensor,
control valve, and actuator.
When the pressure in the air tank rises,
the pressure sensor detects the change and sends a signal to the control valve.
The control valve then adjusts the air supply to the actuator, which in turn
controls the motor speed. As the motor speed changes, the compressor's output
pressure is regulated until it reaches the desired level set by the operator or
system requirements.
Importance of an air compressor governor in maintaining
pressure
Now that we have a better understanding of
how an air compressor governor functions, let's explore the importance of this
component in maintaining pressure. Consistent pressure levels are crucial in
various applications, from powering pneumatic tools to operating industrial
machinery.
Without a governor, the pressure within the
compressor could exceed safe limits, leading to potential equipment failure,
leaks, or even accidents. Conversely, insufficient pressure can result in
reduced performance, inefficient operation, and inadequate power for air-driven
tools and machinery.
By constantly monitoring and adjusting the
compressor's motor speed, the governor ensures that the pressure remains within
the desired range, providing optimal performance and efficiency while
safeguarding the equipment and the operators.
Common issues with air compressor governors
Despite their importance, air compressor
governors can experience issues that affect their performance. Some common
problems include:
1.
Failure to maintain pressure: If the
governor fails to regulate the pressure effectively, it could result in
pressure fluctuations or failure to reach the desired pressure level.
2.
Sticking control valve: Over time, the
control valve within the governor may become sticky or stuck, preventing it
from adjusting the air supply accurately.
3.
Faulty pressure sensor: A malfunctioning
pressure sensor can lead to inaccurate readings, causing the governor to make
incorrect adjustments to the motor speed.
4.
Worn-out actuator: The actuator,
responsible for controlling the motor speed, can wear out over time, leading to
inconsistent adjustments and poor pressure regulation.
Troubleshooting tips for air compressor governor problems
When faced with issues related to your air
compressor governor, it is essential to troubleshoot and address the problem
promptly. Here are some troubleshooting tips to help you identify and resolve
common air compressor governor problems:
5.
Inspect the control valve: Check for any
signs of dirt, debris, or wear on the control valve. Clean or replace it if
necessary to ensure smooth operation.
6.
Calibrate the pressure sensor: If you
suspect an issue with the pressure sensor, recalibrating it may help. Consult
the manufacturer's guidelines or seek professional assistance to ensure
accurate readings.
7.
Check the actuator: Examine the actuator
for any signs of wear or damage. If needed, replace the actuator to ensure
consistent adjustments and proper pressure regulation.
8.
Perform regular maintenance: Regularly
clean and inspect the entire governor assembly, including the pressure sensor,
control valve, and actuator. Lubricate moving parts as recommended by the
manufacturer to prevent sticking or wear.
By following these troubleshooting tips and
addressing issues promptly, you can ensure the optimal performance and
longevity of your air compressor governor.
Choosing the right air compressor governor for your needs
Selecting the right air compressor governor
for your specific needs is crucial to ensure optimal performance and
efficiency. Consider the following factors when choosing a governor:
9.
Pressure range: Determine the pressure
range required for your applications and select a governor capable of
maintaining that range reliably.
10. Accuracy: Look for a governor with accurate pressure sensing capabilities to
ensure precise adjustments and consistent pressure regulation.
11. Compatibility: Ensure that the governor is compatible with your air compressor
model and system requirements. Consult the manufacturer's specifications or
seek professional advice if needed.
12. Durability: Choose a governor made from high-quality materials that can
withstand the demands of your industry and provide long-lasting performance.
By considering these factors and conducting
thorough research, you can make an informed decision when selecting an air
compressor governor.
Maintenance tips for air compressor governors
Proper maintenance is essential to keep
your air compressor governor in optimal condition and prevent potential issues.
Here are some maintenance tips to help you prolong the lifespan and performance
of your governor:
13. Regular inspections: Routinely inspect the governor assembly, including the pressure
sensor, control valve, and actuator, for any signs of wear, damage, or dirt.
Clean or replace components as needed.
14. Lubrication: Follow the manufacturer's guidelines for lubricating moving parts
of the governor. Proper lubrication reduces friction, prevents sticking, and
ensures smooth operation.
15. Calibration: Periodically calibrate the pressure sensor to ensure accurate
readings. Consult the manufacturer's guidelines or seek professional assistance
to perform the calibration correctly.
16. Clean air supply: Ensure that the air supply to the governor is clean and free from
contaminants. Install appropriate filters and perform routine maintenance on
the air filtration system.
By incorporating these maintenance
practices into your routine, you can extend the lifespan of your air compressor
governor and maintain its optimal performance.
Frequently asked questions about air compressor governors
17. Q: Can I use any air compressor governor with my air compressor?
A: It is important to choose a governor that is compatible with your specific
air compressor model and system requirements. Consult the manufacturer's
specifications or seek professional advice to ensure compatibility.
18. Q: How often should I calibrate the pressure sensor in my air compressor governor?
A: The frequency of calibration depends on various factors, including the
manufacturer's recommendations and the operating conditions of your air
compressor. Consult the manufacturer's guidelines or seek professional advice
for the appropriate calibration schedule.
19. Q: Can I repair a faulty control valve in my air compressor governor, or should I replace it?
A: In some cases, a faulty control valve can be repaired by cleaning or
replacing specific components. However, depending on the severity of the damage
or wear, it may be more cost-effective to replace the control valve entirely.
Consult a professional for guidance on the best course of action.
Conclusion: The crucial role of an air compressor governor
In conclusion, the air compressor governor
plays a critical role in maintaining consistent pressure levels within an air
compressor. By monitoring and adjusting the compressor's motor speed, the
governor ensures optimal performance, efficiency, and safety. Understanding the
function and importance of an air compressor governor allows you to
troubleshoot issues effectively, choose the right governor for your needs, and
implement proper maintenance practices. By following these guidelines, you can
optimize the performance and longevity of your air compressor system, ensuring
smooth operations in your industrial applications.
CTA: For more information on air compressor governors and other
industrial equipment, contact our team of experts at [Company Name]. We are
here to assist you in finding the right solutions for your specific needs.