The Impact of Damaged Piston Seals on Air Compressor Performance and Energy Efficiency: Understanding the Price of Inefficient Sealing.
The Impact of Damaged Piston Seals on Air Compressor
Performance and Energy Efficiency: Understanding the Price of Inefficient
Sealing
Introduction to Air Compressors and Their
Importance
Air compressors play a crucial role in
various industries, providing a steady supply of compressed air for a wide
range of applications. From manufacturing plants to construction sites, air
compressors are used to power tools, control systems, and even generate clean
air for breathing. These machines are the workhorses of many operations, and
their efficient functioning is essential for productivity and
cost-effectiveness.
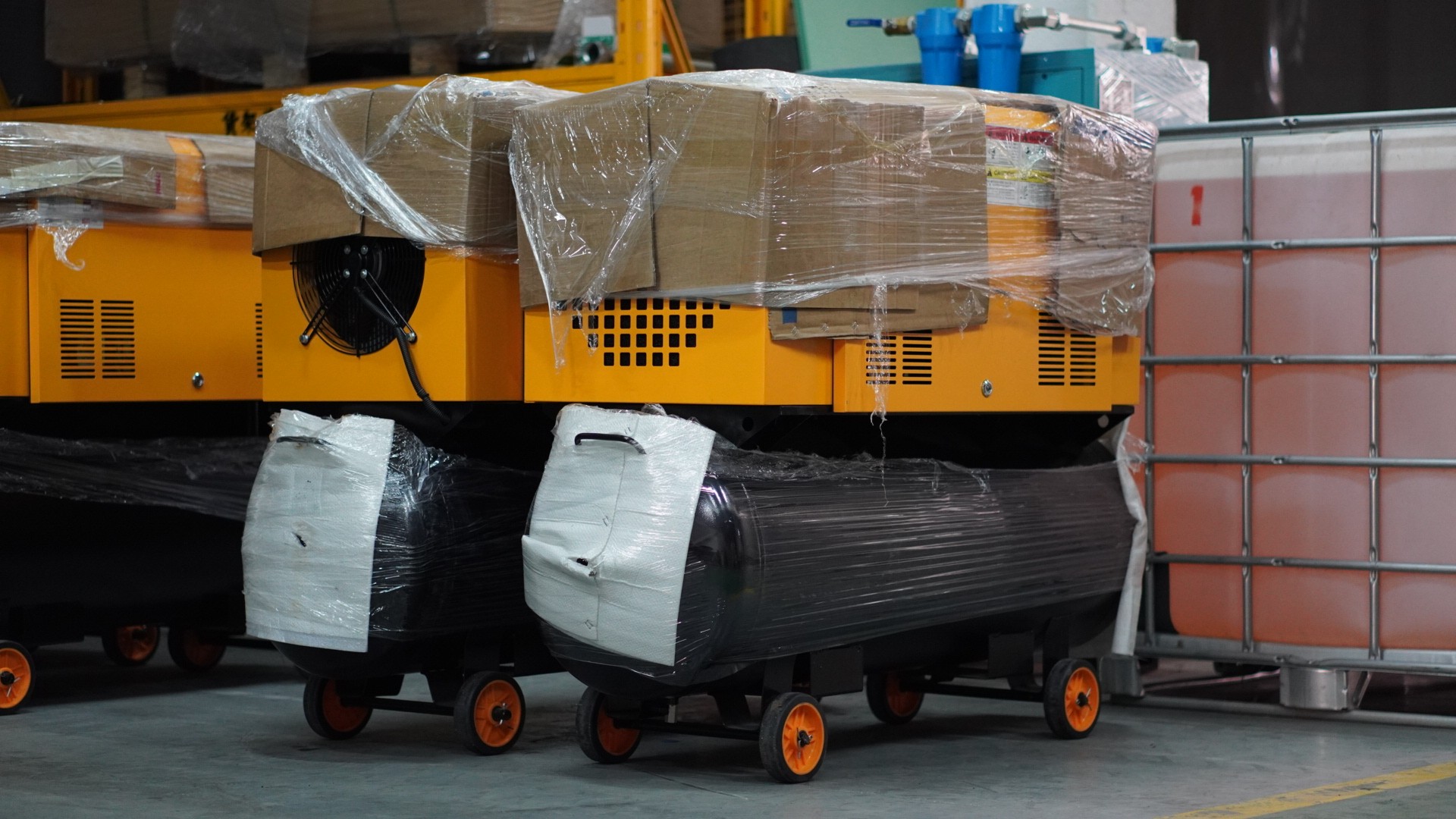
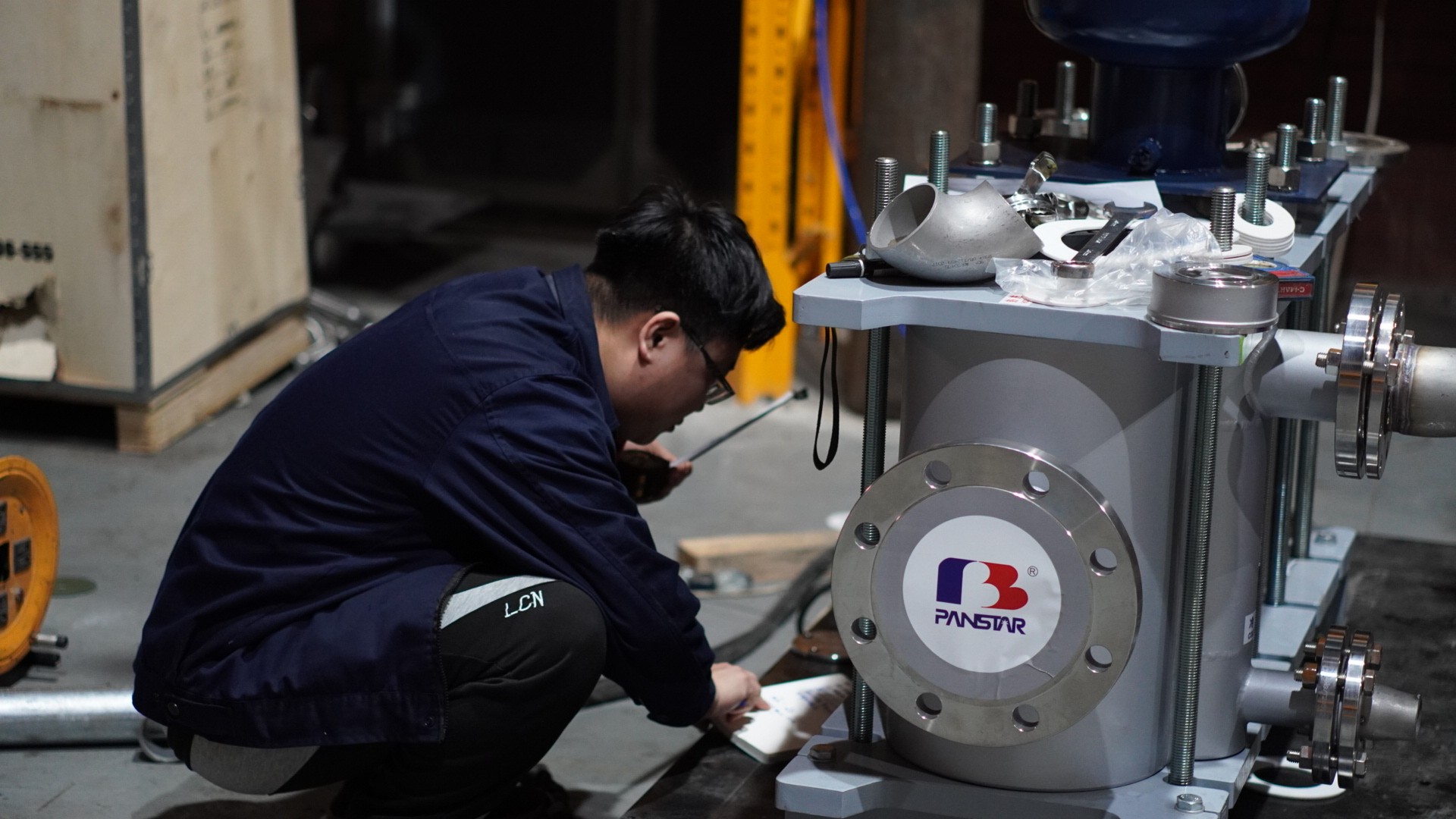
Understanding Piston Seals and Their Role in Air
Compressor Efficiency
Piston seals are a vital component of air
compressors that ensure efficient operation by preventing air leakage between
the piston and cylinder wall. These seals create a tight barrier, allowing the
compression process to occur smoothly and effectively. When piston seals are
damaged or worn out, air leakage can occur, leading to a decrease in
performance and energy efficiency.
Signs of Damaged Piston Seals and Their Impact on Air
Compressor Performance
Identifying signs of damaged piston seals
is crucial for maintaining air compressor efficiency. One common indicator is a
decrease in the overall performance of the machine. You may notice a decline in
the amount of compressed air produced or a decrease in the maximum pressure
achieved. Additionally, if you observe excessive oil consumption or increased
noise during operation, it is likely that the piston seals are compromised.
When piston seals are damaged, air leakage
occurs, leading to inefficiencies in the compression process. This results in
increased energy consumption as the compressor works harder to compensate for
the lost air. Moreover, the reduced performance can affect the productivity of
air-powered tools and systems, leading to longer project durations and higher
costs.
The Relationship between Damaged Piston Seals and Energy
Efficiency
Energy efficiency is a key consideration
for any industrial operation. Damaged piston seals directly impact the energy
efficiency of air compressors. As air leaks occur, the compressor needs to
compensate by working longer and harder to achieve the desired pressure. This
increased workload leads to higher energy consumption and ultimately higher
energy costs.
By maintaining the integrity of piston
seals, air compressors can operate at peak efficiency, minimizing energy waste
and reducing operational expenses. Regular inspection and timely replacement of
damaged seals are essential to ensure optimal energy efficiency.
The Cost of Inefficient Sealing in Air Compressors
The cost of inefficient sealing in air
compressors extends beyond increased energy consumption. It also includes the
potential for costly repairs and premature equipment failure. When piston seals
are damaged, the internal components of the compressor are exposed to excessive
wear and tear, leading to a shorter lifespan.
Additionally, the decreased performance
resulting from inefficient sealing can impact the quality of the products or
services provided by the operation. If air-powered tools or systems fail to
deliver the required performance, it can lead to product defects, rework, or
even customer dissatisfaction. These indirect costs can significantly impact
the overall profitability of a business.
Types of Air Compressors and Their Susceptibility to
Damaged Piston Seals
Air compressors come in various types, each
with its own advantages and applications. Reciprocating compressors, which use
pistons and cylinders, are particularly susceptible to damaged piston seals due
to their design. The continuous reciprocating motion of the piston can lead to
accelerated wear and tear on the seals, making regular maintenance and
inspection critical.
On the other hand, rotary screw compressors
and centrifugal compressors have different sealing mechanisms that are
generally more robust and less prone to damage. However, it is still important
to monitor and maintain the seals in these compressors to ensure optimal
performance and longevity.
Tips for Maintaining Piston Seals and Prolonging Air
Compressor Lifespan
Proper maintenance of piston seals is
essential for prolonging the lifespan of air compressors and ensuring their
efficient operation. Here are some tips to help you maintain piston seals
effectively:
1.
Regular Inspection: Conduct
routine inspections to identify any signs of damage or wear on the piston
seals. Addressing issues early can prevent further damage and costly repairs.
2.
Lubrication: Apply the
recommended lubricant to the piston seals to reduce friction and extend their
lifespan. Follow the manufacturer's guidelines for lubrication frequency and
type.
3.
Cleanliness: Keep the
compressor and its components clean to prevent debris or contaminants from
causing damage to the piston seals. Regularly clean the air intake filters and
ensure proper ventilation around the machine.
4.
Temperature Control: Maintain
suitable operating temperatures to prevent excessive expansion or contraction
of the piston seals, which can lead to premature failure. Install cooling
systems if necessary.
5.
Proper Usage: Use the air
compressor within its specified limits and avoid overloading or prolonged
operation beyond its capacity. This helps minimize stress on the piston seals
and other components.
By following these maintenance tips, you
can maximize the lifespan of piston seals and ensure optimal performance of
your air compressor.
How to Choose a High-Quality Air Compressor Machine
Investing in a high-quality air compressor
machine is crucial for long-term efficiency and reliability. When selecting an
air compressor, consider the following factors:
6.
Capacity and Pressure
Requirements: Determine the required airflow and pressure for your specific
application to choose a compressor that can meet those demands without strain.
7.
Quality and Durability: Look
for well-established brands with a reputation for producing reliable and
durable air compressors. Read reviews and seek recommendations from industry
professionals.
8.
Energy Efficiency: Consider the
energy efficiency rating of the compressor to minimize operational costs. Look
for compressors with features like variable speed drives and energy-saving
technologies.
9.
Maintenance and Serviceability:
Evaluate the ease of maintenance and availability of spare parts for the chosen
compressor. A machine that is easy to service will save you time and money in
the long run.
10. Noise Level: Depending on the environment in which the compressor
will be used, consider the noise level of the machine. Look for compressors
with noise reduction features or soundproof enclosures.
By carefully considering these factors, you
can select an air compressor that meets your specific requirements and offers
long-term efficiency and reliability.
The Price of Efficient Sealing: Investing in High-Pressure
Air Compressors
While the initial cost of high-pressure air
compressors may be higher than their lower-pressure counterparts, the long-term
benefits outweigh the price difference. High-pressure air compressors are
designed to withstand the increased stress and demands associated with higher
pressures, resulting in improved sealing and overall efficiency.
Investing in a high-pressure air compressor
with efficient sealing capabilities can deliver significant energy savings over
time. The reduced energy consumption and increased productivity resulting from
optimal sealing can lead to a substantial return on investment. Additionally,
the extended lifespan of the compressor and reduced maintenance costs
contribute to the overall cost-effectiveness of high-pressure models.
Conclusion: The Importance of Regular Maintenance and
Efficient Sealing in Air Compressors
Inefficient sealing in air compressors can
have a significant impact on performance, energy efficiency, and overall
operational costs. Regular maintenance, including the inspection and
replacement of damaged piston seals, is crucial for maximizing efficiency and
prolonging the lifespan of these machines.
Investing in high-quality air compressor
machines with efficient sealing capabilities, such as high-pressure models, can
result in long-term cost savings and improved productivity. By understanding
the importance of efficient sealing and implementing proper maintenance
practices, businesses can ensure optimal performance and energy efficiency in
their air compressor systems.
Remember, efficient sealing is not just about saving energy and reducing costs; it also contributes to a safer and healthier work environment by minimizing air leaks and preventing excessive noise. By prioritizing regular maintenance and efficient sealing, businesses can enjoy the full benefits of air compressors while minimizing their environmental footprint.